Errors and malfunctions of Candy washing machines
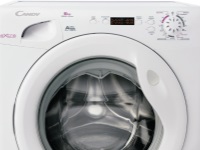
Candy washing machines are good at washing and they please their owners with their small dimensions. A peculiar advantage of such equipment can be called the presence of the error code system. Seeing a certain code on the display, the owner of the Candy machine is able to know what is wrong with the machine and what actions need to be taken in the first place.
Error Codes
Washing machines with display
Code |
What it means |
What's wrong with the machine |
Causes of error |
What to do |
Е01 |
The problem with the hatch lock |
The door does not lock and there is no button indication. |
The locking device is not working or there is a malfunction in the electric controller. There may also be a wiring fault. |
Check door locking device and wiring, then examine electrical controller. Repair or replace defective parts. |
Е02 |
Water priming problem |
The water does not come in at all or the water level does not reach the required values within 210 seconds. This error is also displayed if the water level is too high to allow the command to be carried out. |
The priming valve does not work. The electric controller has stopped functioning. The strainer in the filling system is clogged. The pressostat has stopped working or there is a leak in its connections. |
Check the condition of the valve, the pressostat function and the function of the controller. If necessary, clean the filter in the intake system. |
Е03 |
The problem with water drainage |
Water does not drain at all or takes longer than 3 minutes to empty. |
Drain pump does not work or contacts in its circuits are broken. The pressostat is defective. Drainage path is blocked. |
Check the drainage pipes and hoses as well as the pump and water level sensor. Replace defective parts with working ones. |
Е04 |
The problem with the fill valve. |
Volume of water inside tank exceeds required parameters and as a result pressostat is signalling overflow of tank. |
The fill valve is broken (it stays open all the time) or the electric controller is damaged (often the triac is "to blame" for the malfunction). |
Check the triac and flood valve by repairing them or replacing them with serviceable parts. |
Е05 |
Problem with water heating |
The water is not being heated. |
Temperature sensor, electric controller or heating element is not working. Program selector motor is out of order or control unit circuits are broken. |
Evaluate the efficiency of the heater, measure the resistance of the temperature sensor and the program selector motor. It is also worth checking the electrical circuits and the controller's operability. Replace defective parts with the new ones. |
Е07 |
The problem with the engine |
The engine revolves quickly and abruptly. After three attempts to start it at maximum speed, the washing stops. |
The tachogenerator does not work (most often the problem is with the core). |
Check tachogenerator winding resistance, if defective replace this assembly. |
Е09 |
Problem with the motor |
Shaft stops turning. |
The entire control unit is malfunctioning or the triac has burned out. |
Evaluate the operation of the control unit and the condition of the triac, and if faulty parts are found, replace or repair them. |
Washing machines without display
On models without a display, errors are determined by the number of blinks on the indicator on the bottom left:
Code (number of flashes) |
What it means |
Causes of the error |
Indicator light is on all the time |
Problem with control module |
Control module is not working or a program failure has occurred. |
1 |
Problem with the sunroof interlock |
The locking device is not working or there is a wiring fault. |
2 |
The problem with filling the machine with water |
Inlet valve or pressostat malfunctioned. The priming hose is dirty or pinched. Water pressure in pipes is too low. |
3 |
Problem with water drainage |
Drain pump does not work or contacts in its circuits are broken. Drainage circuit is clogged. |
4 |
Problem with flood valve |
Valve has failed (does not close). Pressostat does not work or its wiring is broken. |
5 |
Problem with temperature sensor |
Sensor malfunctioned due to short circuit or breakage. |
6 |
Problem with EEPROM memory |
Memory error or control module malfunctioning. |
7 |
Problem with the motor |
Drive motor lockout occurred. The hatch lock is stuck (hatch closed). |
8 |
Tachogenerator problem |
Tachogenerator has malfunctioned due to a short circuit or an open circuit. |
9 |
Problem with the drive motor |
Triac burned out. |
12 и 13 |
Communication problem |
The connections connected to the control module are damaged. |
14 |
Control problem |
Control module is not working or its wiring is broken. |
15 |
Control problem |
The control module is not working or its program has malfunctioned. |
16 |
Problem with heating element |
Heater is damaged due to a short circuit. Insulation damage. |
17 |
Problem with tachogenerator |
Tachogenerator is transmitting incorrect signals. |
18 |
Control problem |
Control module does not work or the mains parameters are not suitable for the machine. |
Frequent malfunctions
The most common problems with which the owners of Kandi washing machines turn to masters for repair, are the following:
- Water does not drain from the machine. Most often such a malfunction is caused by a broken pump or clogs in the drain system.
- The machine does not turn on at all or the work of the machine stops at the beginning of the washing process. There are several reasons for such a problem, such as low voltage in the network, loose closing of the door, problems with electronics or a faulty filter.
- Water does not heat up during the washing. Here you should look for problems with the temperature sensor, heater, electronic module, or in the electrical circuits of these units.
- The laundry does not spin. The malfunction may be caused by a clogged hose, overheated motor, broken tachometer, or excessive load of laundry.
- During operation there are unusual sounds, noise and knocking. The causes are varied - from small objects entering the tank and imbalance of laundry in the drum to loose counterweight fasteners or worn bearings.
- During or after a wash, water begins to leak from the machine. This occurs if the pump, the door collar, the fill or drain hose, or the tank is damaged.
- Water does not pour into the drum of the machine due to a clogged filter, malfunction of the pressostat or other reason.
About Candy washing machine repair with error E05, see the following video.
Tips and prevention of breakdowns
- Regularly clean the outside of the machine, but do not use agents with solvents, alcohols or abrasive particles. To clean the machine, just use a damp cloth.
- Inspect the detergent container after each wash, removing detergent residue (this will prevent it from drying in the container) and before each subsequent wash. If necessary, remove the container, rinse under running water and return it to its place.
- At least once every 6 months, inspect and clean the Candy appliance drain system. To clean the filter, use the instructions you will find in the machine's manual.
- If the machine needs to be moved or if it will not be used for a long time, all water from the machine should be drained.
For a long life of your helper, do not forget to clean it and carry out preventive measures, told in the Ukrainian program "Everything will be good".