Errors and malfunctions of Whirlpool washing machines
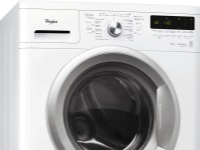
Whirlpool machines belong to the medium price category models, so they are of high quality and long service life. But like any appliance from other manufacturers, a washing machine can break down over time. To tell you exactly what happened to your machine, you can use the codes that appear on the machine's display for various malfunctions.
Error codes
Code |
What it means |
Causes of the error |
What to do |
F01 (FH) |
There is a problem with water supply into the unit |
The water pressure in the water pipes is too low and is therefore not coming at all or not as much water as necessary. |
Check the water pressure in the pipes. |
There is a clog in the fill valve screen or the water supply tap is not fully unscrewed. |
Make sure that the tap is completely unscrewed and the filter is not clogged. |
||
The sensor which detects the water level has stopped working. |
Check the operation of the pressostat and the solenoid valve, as well as the drain pump. |
||
Contacts of pressostat, priming valve or drain pump are broken. |
Clean contacts of pressostat, priming valve or drain pump. |
||
Controller malfunction. |
Evaluate controller operation by checking circuits and contacts. |
||
F02 (FA) |
AquaStop on. |
The solenoid valve responsible for pouring water into the machine is blocked. |
Repair or replace the solenoid valve with a new part. |
The electric controller is malfunctioning. |
Fix the controller defect or replace it. |
||
Water leakage has occurred. |
Check machine components for leaks, repair leaks and replace damaged parts. |
||
F03 (FP) |
The appliance has a problem with water drainage |
Water does not drain from the machine because the drain pipe is broken or clogged. |
Inspect the drain path by checking its permeability, then remove the dirt or repair the damaged parts. |
The pump that pumps water out of the machine is broken. |
Clean the pump filter and check its contacts, and if repair is impossible, replace it with a new pump. |
||
The parts on the circuit board of the electric controller have burned out. |
Once you are sure there is a problem with the controller, replace the controller itself or the parts that are burned out. |
||
F04 |
Problem with water heating |
Water is not heated to the correct temperature due to breakage of the heating element due to scale formation on the surface of the heater. |
Inspect the heater, clean it from scale or replace it with a new part. |
The temperature sensor control circuit is damaged. |
Check temperature sensor control circuit by replacing damaged parts or repair breakage. |
||
Open circuit in temperature sensor or damage caused by short circuit. |
Evaluate the operation of the temperature sensor and replace it if it is damaged. |
||
F05 |
Water heating problem |
The temperature sensor is malfunctioning. |
Test temperature sensor circuit. If necessary, replace damaged wires and seal contacts. If the sensor itself is defective, you will have to replace it with a new one. |
F06 |
No signal from tachogenerator |
Tachogenerator assembly with spring washer is defective. |
Reinstall the loose washer. |
Communication between control board and tacho is broken (circuit damaged). |
Repair the circuit between the motor control board and the tacho. |
||
F07 |
Problem in the motor control board |
The electronic controller does not work. |
Repair the controller or replace it completely. |
Triac flash or thyristor burned out in control board. |
Replace all burnt-out parts on the control board. |
||
F08 |
Problem with heating element |
Heater burned out or wire breakage in heater wiring. |
Replace or repair heater wiring and check contacts. |
Protective pressostat is broken. |
Replace damaged pressostat. |
||
The electric controller is defective. |
Replace the damaged controller or repair the board and replace the burned-out elements. |
||
Thermistor appears damaged. |
Re-solder thermistor or seal contacts in thermistor circuit. |
||
F09 |
Problem with water inlet |
The sensor that controls the water level has malfunctioned. |
Repair the hydraulic sensor system or replace the pressostat. |
Faulty or blocked water priming valve. |
Replace the priming valve with a serviceable part. |
||
Controller malfunction. |
Check controller, resolder burned out parts of controller board or replace controller with new one if it is impossible. |
||
F10 |
Problem with electric motor |
Motor does not turn on due to triac burnout on the control board. |
Examine the control board and replace the parts that have burned out. |
Thermosensor in the motor module has failed. |
Replace the thermosensor, or if it cannot be repaired, install a new control module. If this does not work, you will have to replace the motor itself. |
||
F11 |
Communication problem |
The power supply voltage is below the required level. |
Check the voltage and take measures to restore the normal parameters of the apartment's electrical system. |
F12 |
Water heating problem |
The water is no longer being heated due to a defective heating element or a broken pressostat. |
Replace the defective heating element or the pressostat. |
There is a break in the wires between the heating element and the controller. |
Check the wires between the controller and the fuel dispenser, repair the detected defects, and seal the terminals. |
||
The water heating relay has malfunctioned (jamming has occurred). |
If examination confirms the problem in the heating relay, it should be replaced with a new one. |
||
The temperature sensor has malfunctioned. |
After confirming that the temperature sensor is damaged, repair the control board by replacing the thermistor. |
||
F13 |
Problem with water inlet |
Water does not fill the tank due to insufficient water pressure in the water supply line. |
Check the water pressure in the water supply line. |
Detergent loading container is clogged. |
Perform cleaning of the detergent tank. |
||
Water is drawing in too slowly due to a clogged strainer in the filler valve. |
Clean the strainer in the filler valve. |
||
F14 |
Problem with control system |
The control board has started to run with errors. Microprocessor error has occurred. |
Reprogram the controller or replace the entire control unit of the machine. |
F15 |
Problem with electric motor |
Triac fault on controller board. |
Check triac operation and replace if faulty. |
The motor brushes are worn out. |
Replace the brushes or replace the entire motor. |
||
Tachogenerator mechanical component malfunctioned. |
Repair tachogenerator by replacing spring washer. Sometimes the tachogenerator needs to be replaced with a new part. |
||
There is a break in the wires connecting the motor to the controller. |
Check wires and replace wiring sections where problems are detected. |
||
The electrical controller is defective. |
Repair controller board or replace controller completely with new part. |
||
F16 |
Problem with control system |
Damage has occurred in the wires. |
Inspect the contacts and check the wires by stripping and replacing the defective parts. |
Parts on the control board are burned out. |
Repair the control module or replace it completely in the washing machine. |
||
F18 or Fod |
Incorrect detergent |
Detergent has been loaded into the machine causing excessive foam formation. |
Change the detergent and restart the machine. |
F19 |
Problem with the power supply |
The mains voltage is incorrect (too low or too high). |
Normalise the mains voltage and restart the machine. |
F20 |
Problem with controller |
The control program cannot run due to a malfunction of the control unit. |
Restart the machine, and if the washing does not start, check the operation of the control unit, try to repair the controller board, and if this is not possible, replace the controller completely. |
F21 |
Problem with controller |
Command transmission from controller to control module has been disrupted due to wiring and contact problems. |
Inspect wiring and repair defective areas. Seal contacts and tighten wire clamps. If the problem persists, replace the controller. |
F22 |
Water supply or heating problem |
The heating element is not heating the water. |
Inspect the heater by sealing its terminals. If necessary, replace heater with a new one. |
Contacts between the heater and controller are broken. |
Test the wires and pay attention to the sealing of the terminals. |
||
Domestic power supply voltage is insufficient to operate the heater. |
Turn off the machine and correct problems in the power supply. |
||
Water cannot pass through the detergent tank because it is clogged. |
Check the condition of the tank and clean the clog found. |
||
F23 |
Problem with water inlet |
The water level sensor is malfunctioning, resulting in simultaneous signals of the tank being full and the tank being empty. |
Check the pressostat and replace with a new part if there is a problem. |
F24 |
System malfunction that controls the water level in the tank. |
The water level sensor is broken, causing it to give overflow signals. |
After confirming the malfunction, replace the pressostat. |
F26 |
Problem with the electric motor |
A triac in the control board has stopped the motor from rotating due to a fault in the triac. |
Replace the triac and check the contact tracks on the board. |
F27 |
Problem with electric motor |
The reversing relay on the control module board is defective and the motor only rotates in one direction. |
Check the reversing relay, and if it is broken, replace it with a working part. |
F28 |
Problem with the electric motor |
The winding change relay is defective, causing the motor to rotate too slowly, or the motor to stop starting during cycle changeover. |
Check the relay and replace it. |
F31 |
Problem with software update |
The software cannot be updated through the internet. |
Contact your service provider. |
FDL |
The problem with the sunroof |
The hatch lock has failed. |
Check the contacts of the hatch lock by cleaning and tightening them. If repair is not possible, replace the interlock. |
FDU |
Problem with the hatch |
The door is not properly closed. |
Open the door and try to close it more tightly. |
The door lock is defective. |
Repair or replace door locking device. |
Frequent malfunctions
Statistics of malfunctions of Whirlpool machines show that the most frequent problems are the following:
- Clogged drainage path.
- The pump wears out and breaks.
- The electronic control board fails. More often the triacs burn out or the mechanical control unit wears out.
- Heater or thermostat breaks down.
- The tank gasket, nipples or cuffs begin to leak.
- Engine brushes wear out.
- The drive belt breaks.
- The motor contacts burn out.
- Bearings or shock absorbers wear out.
- Foreign matter enters the machine.
About replacement of flanges of the drum, bearings in the washing machine Whirlpool look in a video of V.Khatuntsev.
Tips and prevention of breakdowns
- For external cleaning of the machine body and control panel, use a slightly damp soft cloth. If necessary, the cabinet can be cleaned with a neutral household cleaner which does not contain abrasive particles.
- When the washing cycle is completed and the laundry is removed, the door should be left open for a while to allow the interior of the appliance to dry.
- If you do not wash your laundry at a high temperature, or if this washing is quite rare, sometimes run a program that provides for heating water to +95 ° C, loading a little detergent into the tank. Such a procedure will clean the internal parts of the machine.
- Since Whirlpool washing machines have a filter to trap foreign objects that may get into the machine with the laundry, it should be checked and cleaned regularly - at least 2-3 times a year. To do this, first drain the water, then remove the filter and clean it, as well as the compartment in which it is located. After inserting the filter back and screwing it all the way clockwise, pour about a liter of water into the drum to check the tightness. Now you can close the lid and connect the machine to the mains.
- To prevent deposits from accumulating in the detergent dispenser, at least 3-4 times a year it should be removed from the machine and rinsed under running water.
- Inspect the cover gasket on a regular basis. It is advisable to wipe it with a wet cloth.
- Perform regular inspections of the fill hose to detect cracks and areas of brittleness in time.
- Inspect the fill hose filter at least 2-3 times a year to clean it if necessary. It is not recommended to submerge the filter in water. A good option is to use an old toothbrush to clean it.
To prevent breakage, it is necessary to perform a number of simple actions that will significantly extend the life of your helper. These measures are universal and suitable for any brand of washing machine.