Errors and malfunctions of washing machines Siemens
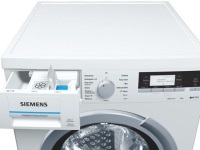
Siemens brand appliances have proven themselves with the best side, but even such high-quality and reliable washing machines break down from time to time. So that the owner of the machine can quickly understand what happened to the appliance, the equipment from Siemens provides a diagnostic system. The error code appears on the display of the machine, deciphering it, you can understand what the problem is, whether it is realistic to fix the machine by yourself or you need to call a specialist.
Error codes
Code | What it means and the possible reasons | What to do |
F01 | Door not closed tight enough. | Check the door and close it more securely; if the laundry is in the way, remove some items from the appliance. |
F02 | No water supply due to:
| Identify and remove blockage in hose and check water supply. |
F03 | No water drainage due to:
| Clean the filter and the drainage system connections, as well as check the pump and its impeller for freedom of rotation. Replace a defective pump with a working part. If there is nothing wrong in the drain assembly, check the electric controller. |
F04 | There is water leakage. | Check connections and tightness of the tank in search of the source of leakage. |
F16 | The door is not closed and this prevents the program from starting. | Open the door and close it again and restart the washing program. |
F17 | Water is taking longer to arrive than necessary due to:
| Check the faucet through which water enters the machine, as well as the water pressure. Inspect and clean the filter in the water inlet hose. |
F18 | Water takes longer to drain than necessary due to:
| Inspect the drainage system and clean the clog in the drain pump, and if it is defective, replace this part. Check the pressostat and its switch, and if this sensor is the problem, replace it with a working one. |
F19 | The water takes longer to heat than necessary because of:
| Inspect the heater and associated wires, and if the heater is out of order, replace it or call a specialist. |
F20 | Unscheduled activation of heater due to:
| Inspect NTC sensor and FET, and replace faulty elements. |
F21 | Control system malfunction, as the result of which the motor operates irregularly and the drum does not rotate. The situation is possible in case of:
| Check the drive motor, the tachogenerator and the control unit for proper operation, and repair or replace faulty parts. |
F22 | The temperature sensor is not working due to:
Washing does not stop, but water is not heated. | Replace faulty sensor or repair its wiring. |
F23 | Aquastop has been activated as a result of:
| Inspect all parts of the machine that may be leaking and check the correct operation of the Aquastop and its connection circuits. |
F25 | The Aquastop is not working because of:
Washing will not stop, but the rinse cycle will be skipped. | Clean the drainage system and the sensor, and if necessary, replace the pressostat with a defective part. |
F26 | An analogue pressure sensor is defective or the pressostat is broken. This error can also be caused by a break in the connection circuits of these sensors. | Disconnect the machine to inspect the sensors and their electrical circuits and then replace damaged and faulty elements. |
F27 | Pressostat not correctly set. | Carry out the correct setting of the sensor, check that it is in good condition and check its connections. |
F28 | Flow sensor doesn't work. | Evaluate the operation of the sensor and its wiring, and if any faults are found, replace the parts that are not working. |
F29 | Flow sensor can not detect water intake due to:
| Make sure that the faucet is open, then check the water inlet system of the machine as well as the connecting circuits connected to it. Replace the defective parts with new ones. |
F31 | The water level is higher than normal due to
| Check that the solenoid valve, drain pump and pressostat are working properly and that the drain hose is not pinched or dirty. If all components are OK, check the wiring. |
F34 | The door cannot be closed because:
| Disconnect the machine, then check the door lock, determine the mechanical obstacles to closing, and check the wiring. |
F36 | Door lock does not work because relay is broken or triac is burned out. | Reset the washing program by disconnecting the machine, then check the control module and wiring. |
F37 | Temperature sensor doesn't work (because it is broken or there is a break in the connections). | Replace the faulty sensor or repair the wiring. |
F38 | The temperature sensor does not work (due to a short circuit). | Replace the faulty sensor or repair its wiring. |
F40 | Problem in the power supply network (unacceptable parameters). | Check the mains supply and correct the parameters. |
F42 | Due to triac burnout in the electronic module, the motor started to run at high speed uncontrollably. | Switch off the machine, test the program and check that the electronic module is working correctly. |
F43 | Motor stops rotating due to
| Disconnect the machine, run the test program, then correct the laundry load, tachogenerator operation, wiring and electronic module. |
F44 | No motor rotation in reverse, often caused by breakage of reversing relay or triac burn-out in electronic module. | Disconnect the machine, test the program and check that the electronic module is working correctly. |
F59 | There are problems with the operation of the 3D sensor due to:
| Check the operation of the sensor, power module, as well as wiring, and then replace the damaged and faulty elements. |
F60 | Flow sensor does not work due to broken sensor itself or clogged fill system. | Check the permeability of the fill valve, the operation of the flow sensor and its wiring, and if any faults are found, replace the parts that are not working. |
F61 | Wrong signal from the door because it is not closed properly, the lock is broken, or the wiring is damaged. | After resetting the error, check the hatch tightness, door lock and electrical circuits one by one. Replace the parts and wiring if any are faulty. |
F63 | Functional protection disturbed because of processor malfunction or software error. | After canceling the program by turning off the machine, check the power module and if it is defective, replace it. |
F67 | Incorrect coding of the card. | After cancelling the program by switching off the machine, make a correct coding or replace the card. |
Е02 | The motor doesn't work | Check winding resistance and brushes one after the other, then check the connections and finally check the control module. Replace the defective parts with the new ones. |
Е67 | Problem with the module's coding (often the firmware is faulty) | Contact a specialist who will reprogram the module. Alternatively replace the module with a new one. |
Frequent malfunctions
Most often the owners of Siemens brand machines turn to the masters of repair for the following reasons:
- Damage to the rubber spigots.
- Breakdown of the drain pump.
- Failure of the heating element due to scale.
- Mechanical damage of the hatch.
- Wear of the bearings.
- Control module burnout.
About the replacement of the manhole collar, TEN and drain pump in a Siemens washing machine, see the video of Remstirmash company.
Tips and prevention of breakdowns
- If you want to clean the outside of the machine, be sure to unplug the machine, do not direct the water jet at the machine and do not use household chemicals with solvents or abrasive particles. It is best to simply wipe the machine with a damp soft cloth.
- To remove limescale from the machine's components, only use products specifically designed for this purpose and in accordance with the recommended dosages.
- Regularly inspect the detergent tank. If you see dirt or powder residue in the flask, remove the flask, rinse, and return it to the machine.
- Check the condition of the suction pump several times a year. To do this, remove the plinth panel, remove the drain hose and drain the water, then clean the pump and check the rotation of its impeller. After closing the pump with the cover, fasten the base plate.
- At least once a year you should remove and inspect the strainer, which is located in the water supply hose to the machine.
The preventive measures shown in the Ukrainian program "All will do good" will help increase the life of your washing machine.